New Distribution Center, Software Vastly Modernizes Medical Storage in Haiti
Posted on Jan 18, 2018
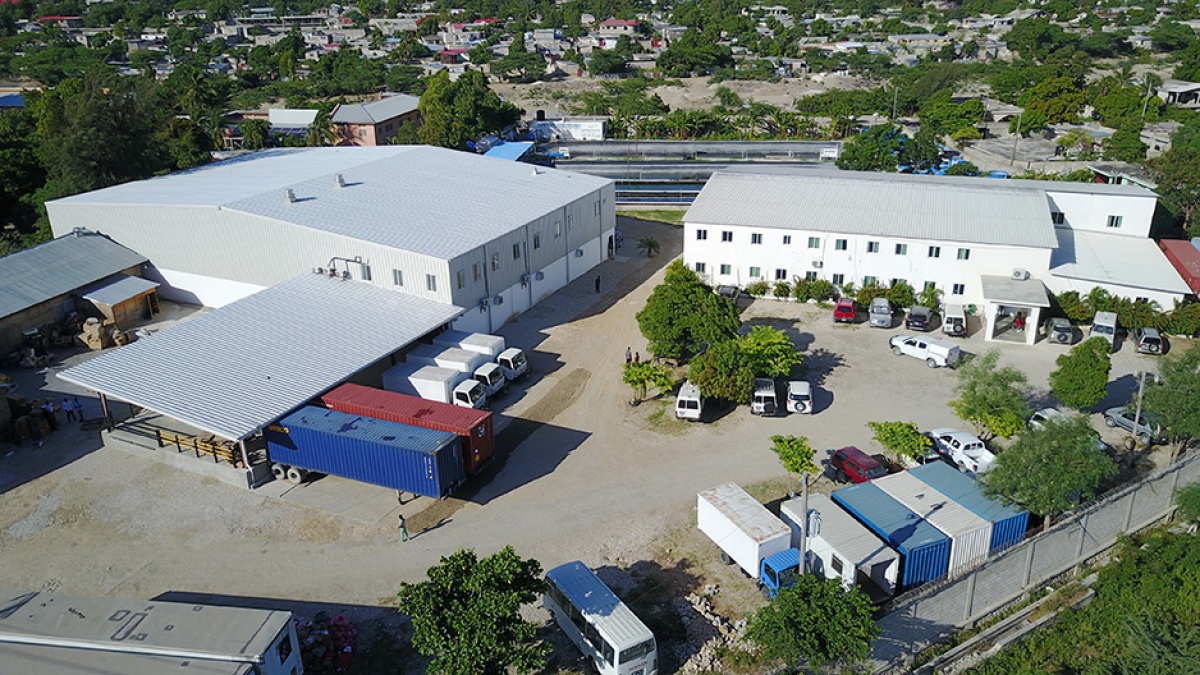
Around noon one day last November, an industrious group of workers opened boxes within the cavernous, climate-controlled distribution center at Partners In Health’s headquarters in Port-au-Prince, Haiti. A forklift operator hauled in a pallet of supplies to be inventoried and placed on floor-to-ceiling shelves. One story above, more employees plugged away on laptops in a refreshingly air-conditioned space, while colleagues ate leftovers in an adjoining lunchroom.
Nothing about this scene seems extraordinary. That is, unless you consider the immense obstacles formerly faced by employees at Zanmi Lasante, as PIH is known in Haiti.
A temporary plywood warehouse used to be PIH’s central storage facility. Temperatures often exceeded 100 degrees Fahrenheit. There was never enough space, so boxes of new supplies got stacked wherever there was room. Drugs that required temperature control had to be stored in two off-site locations so they wouldn’t spoil. Unloading freight or loading trucks bound for PIH clinics and hospitals took days instead of hours, because there was no shelving or way to track the materials’ location within the warehouse—beyond workers’ collective memory, at least.
All that changed with the new distribution center’s opening last May.
“Day to night—nothing comparable,” Villarson Avignon, supply chain director for PIH in Haiti, said about the difference the building has made for his team.
The new distribution center is a 17,000 square-foot, state-of-the-art facility that has dramatically increased central storage capacity and helped modernize how inventory is maintained. A 14,000 square-foot storage room occupies most of the space, a third of which is climate-controlled for temperature-sensitive medication. Another 2,900 square feet is mezzanine office space. And a covered loading dock that blocks the sun and torrential rains—depending on the season—has enough space to park three shipping containers and three trucks.
While the distribution center was a major milestone, Avignon acknowledged it only stored 60 percent of the total volume of supplies and medicine that PIH facilities required. He and his team still rely on the dilapidated plywood warehouse, built as a temporary solution in 2012, for storage of less fragile stock. He could really use another 17,000 square feet of fortified storage space, and dreamed of the day PIH might reach that goal.
PIH broke ground on the new distribution center in June 2016, and employees watched the two-story structure fill out over the following year. In April 2017, Avignon and his team began moving materials into the nearly finished space and updated the inventory in OpenBoxes, an open source software system that PIH developed and uses in several countries to track the movement and storage of supplies. The Port-au-Prince facility and University Hospital in Mirebalais were the first to use the software, which was updated so that employees could record shelf location. Now, everything—from sterile gloves and lab tests to vitamins and surgical supplies—has an easily trackable location within the distribution center.
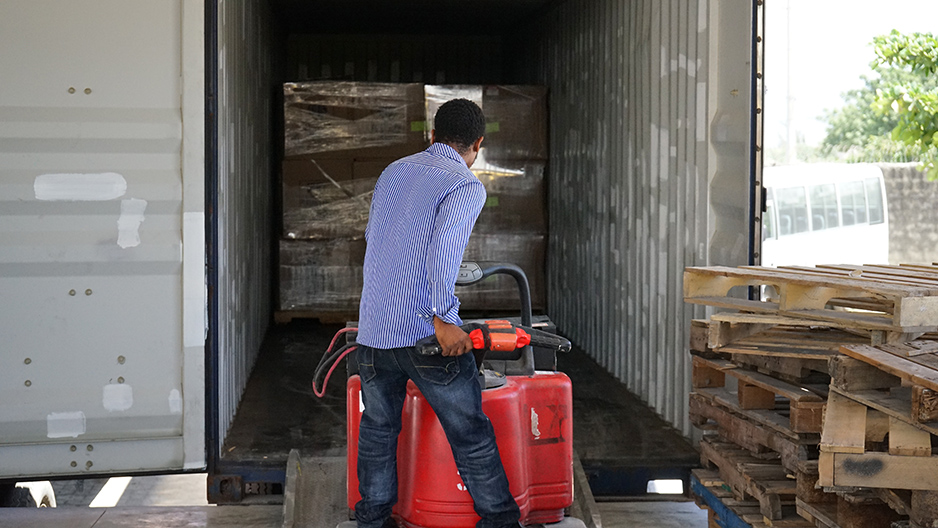
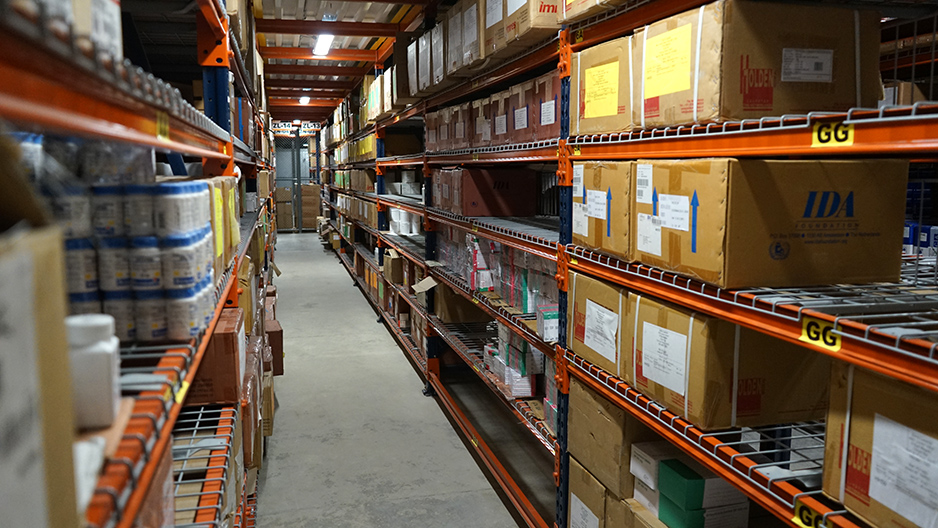
“Today we know exactly where we put our inventory,” Avignon said. “We can receive two containers and prepare three trucks to make deliveries to sites at the same time.”
Previously, it would take his team two days to unload just one container. Packing trucks for sites also now takes less time, which means necessary supplies get to where they are most needed right away.
“The difference is huge,” Avignon said.
Jesse Greenspan, a senior supply chain manager for PIH in Boston, said PIH imports much of what it needs for health facilities in Haiti. All materials and medications travel, through a hub-and-spoke model, from Port-au-Prince out to PIH’s 12 sites across the Central Plateau and lower Artibonite. More than 400 deliveries arrived at the Port-au-Prince facility in 2017 alone, including 80 40-foot shipping containers each weighing up to 67,200 pounds.
Boston and Haiti staff next want to improve storage and inventory practices at outlying clinics and hospitals. Many of those facilities have depots that need shelving and air conditioning to protect temperature-sensitive stock. And many staff still use paper and Excel spreadsheets for record-keeping. A PIH software engineer is tweaking OpenBoxes to make it more user-friendly and improve the efficiency of data collection.
Once in place, these adjustments will lead to a more efficient distribution system from Port-au-Prince out to PIH-supported facilities. Clinics and hospitals will have the essential medications and supplies on hand. And staff will have the tools they need to place more accurate orders based on reliable data.
These small changes are significant, as was the investment in a state-of-the-art distribution center. Ultimately, they all translate into better and more consistent care for patients.