Working in Global Health: Advice from PIH’s Kathryn Kempton
Posted on Mar 17, 2014
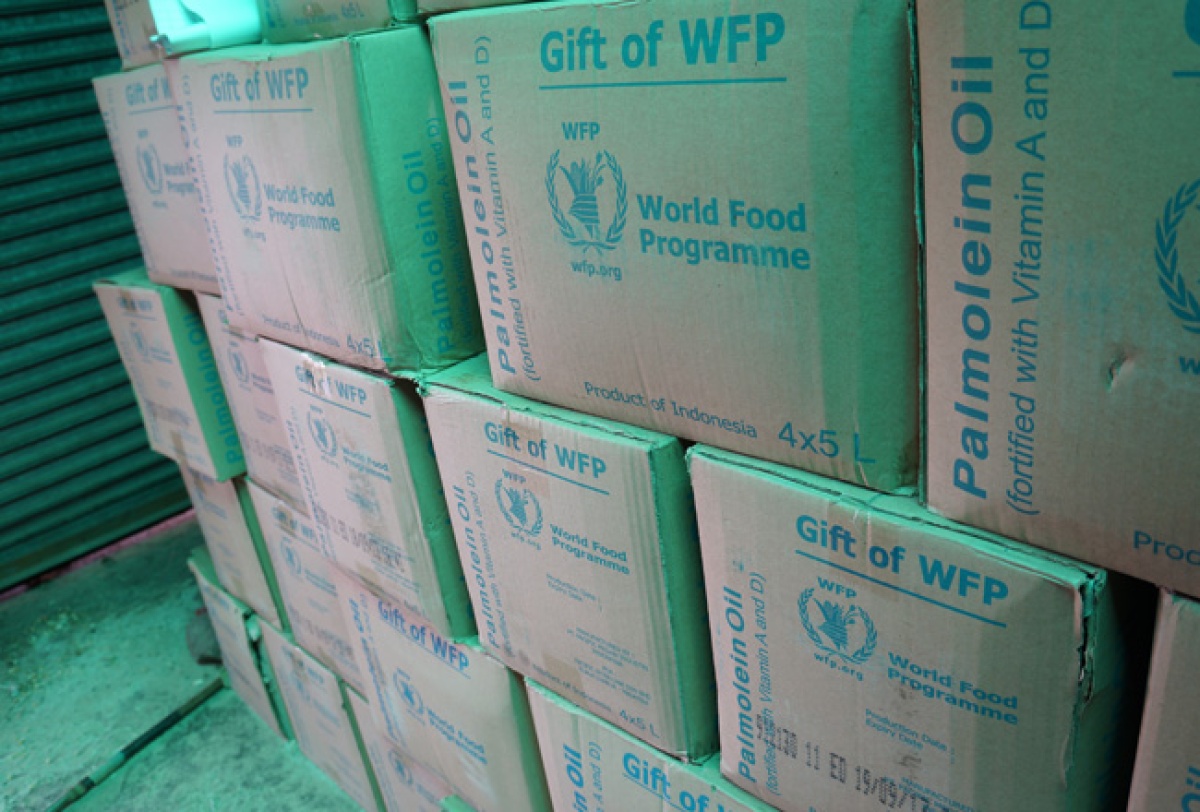
Starting a career in global health can be intimidating. It’s a diverse field that evolves quickly and demands collaboration across disciplines, from finance to supply chain and logistics, to computer programming.
Each month we ask a seasoned colleague to share advice for those interested in forging a career in global health. This month we asked International Operations Director Kathryn Kempton.
I stood in the cold hangar at Massachusetts’ Hanscom Air Force Base in the early morning light, staring down the half-dozen anesthesia machines. The shrink-wrap had compressed hoses and cables securely into place, but the machines still measured about six feet tall and three feet wide. Nearby hospitals had donated the anesthesia units for immediate deployment to Haiti. They were desperately needed in the makeshift operating suites in Port-au-Prince to increase our ability to treat those injured in the devastating earthquake a few days earlier.
I looked over my shoulder at the jet. Sizing up the steep stairs and the plane’s narrow doorway to which they led, I felt a wave of frustration and defeat. There was no way these machines could get onto the plane. In all the arrangements we’d made to get this first group of surgeons, nurses, and equipment to Haiti, it never occurred to me to ask about doorway clearance.
In my defense, I’m not a disaster response specialist or a trained logistician. But as the director of international operations at Partners In Health, my team and I have often been asked to overcome the seemingly impossible. Whether it’s getting a suitcase of medications to a physician’s home the night before a flight to Africa or finding a safe way to send restricted, hazardous materials to Haiti, our team is called on to solve problems quickly and creatively. This was never truer than in the aftermath of the 2010 earthquake in Haiti, which forced everyone at PIH to create new systems and develop new skills.
The urgency of our work demands that we’re flexible, creative, and tenacious.
Whether we’re responding to a natural disaster or just handling day-to-day crises, the international operations team is responsible for the purchase of medicines, supplies, equipment, spare parts, and all the other materials that keep our clinical facilities running. Think of us as the “stuff” people. Because we work in resource-limited settings where many commercial goods are unavailable, the range of items to procure extends far beyond medical materials. Over the years, we’ve purchased and shipped everything from blood collection tubes to flashlights, from construction materials to fish food for the hospitals’ koi ponds.
I work out of our Boston office, where our team is based. From here we can interface with our colleagues in the PIH sites and with the dozens of vendors, freight forwarders, and international partners with whom we work. We’re also positioned to manage inventory, monitor stock levels, dispatch shipments to our hospitals and clinics, and field requests from the sites. In most PIH country sites, we employ local operations staff that handles importation and customs clearance.
Our team members have diverse and broad experience. Some are returned Peace Corps volunteers with deep knowledge of developing countries. Others have backgrounds in domestic project management. Some, like me, came with little formal training and have learned on the job. I had the unique opportunity to grow into my role concurrent with the growth of PIH’s global footprint. As the need for essential medicines increased in Haiti, I learned about international vendors and wholesale purchasing. When PIH expanded our drug-resistant tuberculosis work in Peru and Russia, I learned how to navigate global drug markets, patent laws, and concessional pricing for developing countries.
We’re hands-on people who like to get into the details of a situation, understand it, and devise solutions and improvements.
Regardless of our professional and educational backgrounds, there are universal traits found in those drawn to operations work. Everyone on the team is a “do-er.” We’re hands-on people who like to get into the details of a situation, understand it, and devise solutions and improvements. We are systems-focused, constantly looking for more efficient strategies. Often we play a detective role; when a colleague in the field sends a cryptic message like, “I need a cable for the ultrasound machine,” it’s up to us to extract the information we need from our records and from our colleague, then identify suppliers and find the right part—preferably at a discounted price. The urgency of our work demands that we’re flexible, creative, and tenacious.
Although we do not sit with patients in exam rooms, our work directly affects the delivery of health services. Before a new piece of equipment is purchased, our team researches past performance and analyzes its suitability. What are the power needs—will a converter or inverter be needed? Is it durable and able to withstand heat, dry conditions, humidity? Is it compatible with existing equipment? Will the staff using the equipment be able to receive training, technical support, and maintenance?
This work takes time but we know firsthand the problems that arise when these kinds of questions are not asked. By focusing on assessment and careful selection, the international operations team has built an extensive body of knowledge about hospital systems, including oxygen generators, neonatal equipment, and pathology laboratories. We are able to share our experience with other PIH sites, both to avoid repeat mistakes and to strengthen and eventually standardize the equipment used in PIH locations globally. Every day new challenges are presented, and every day we learn how to improve our work.
Through some miracle—or sheer force of will—we managed to get one of the anesthesia machines onto that jet at Hanscom Air Force Base. In the following week, all of the other units found their way to Haiti, along with the tubing, vaporizers, and medications necessary to make them work.
And now, importantly, we’ve added another item to the ever-growing list of questions we ask: the clearance of an airplane’s door.